Our Work
Experience in action
Each of our projects benefits from our decades of expertise and is the culmination of rigorous planning, development and execution. Most important, each is the tangible result of a powerful relationship with a client — a collaboration that often begins the moment a liquid storage project is first considered and continues over the lifetime of the completed tank. Spanning Water Storage, Wastewater Storage, Concrete Tank Services, and Thermal Energy Storage — and impacting communities across the country — explore how we’re fulfilling our mission to deliver the highest quality liquid storage tanks at the best long-term value.
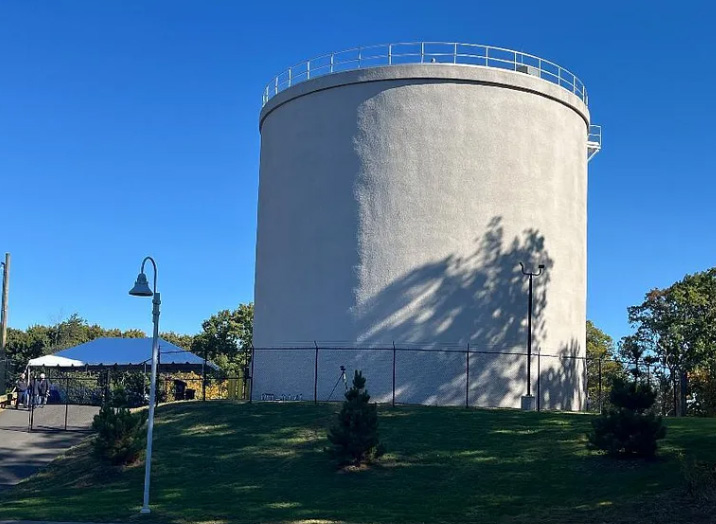
1.0 MG Gound Storage Tank Derby, CT
Derby, CT
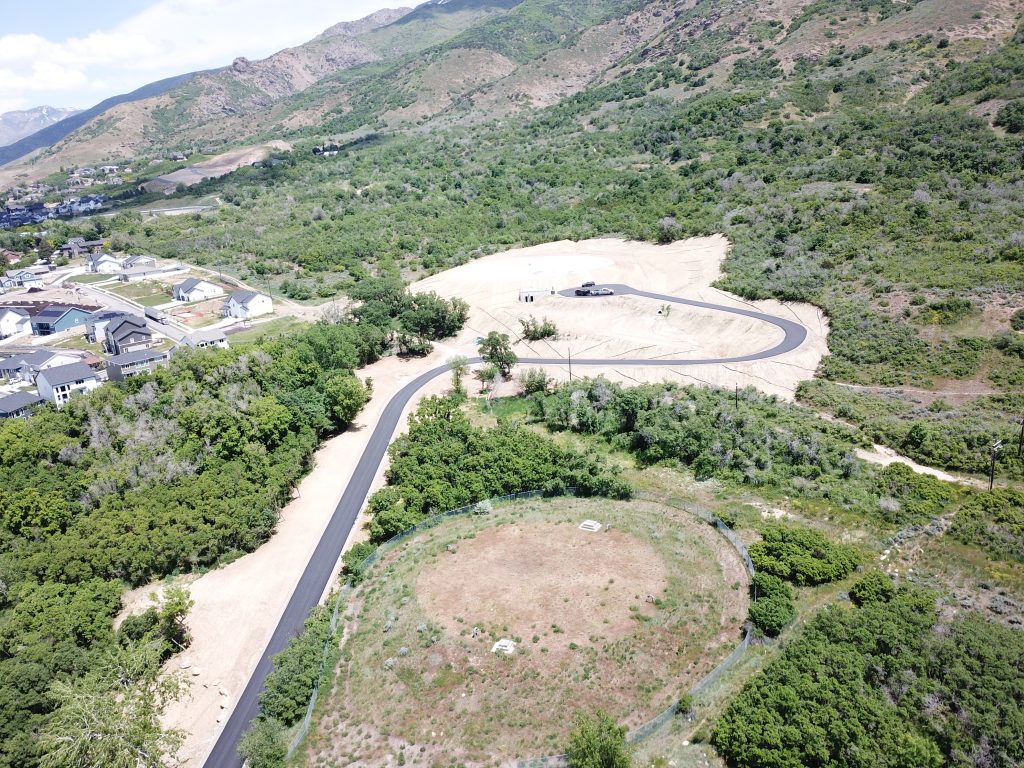
5.8 MG Ground Storage Tank in Kaysville, Utah
Kaysville, UT
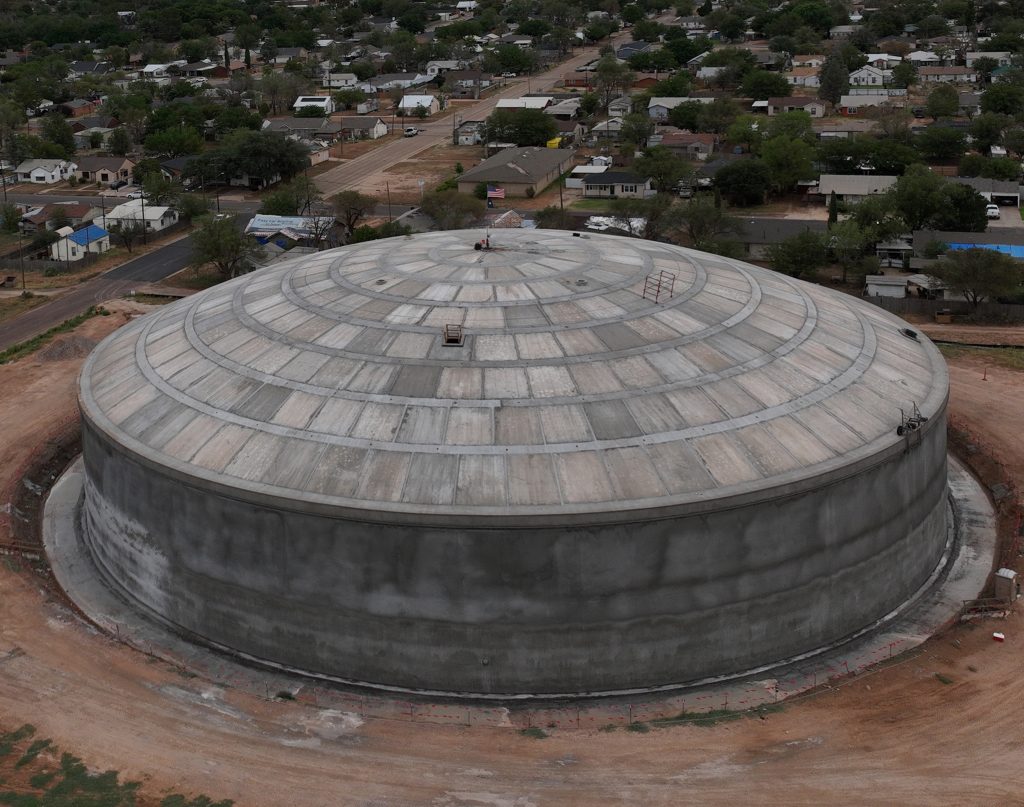
14.0 MG Ground Storage Tank in Lamesa, TX
Lamesa, TX
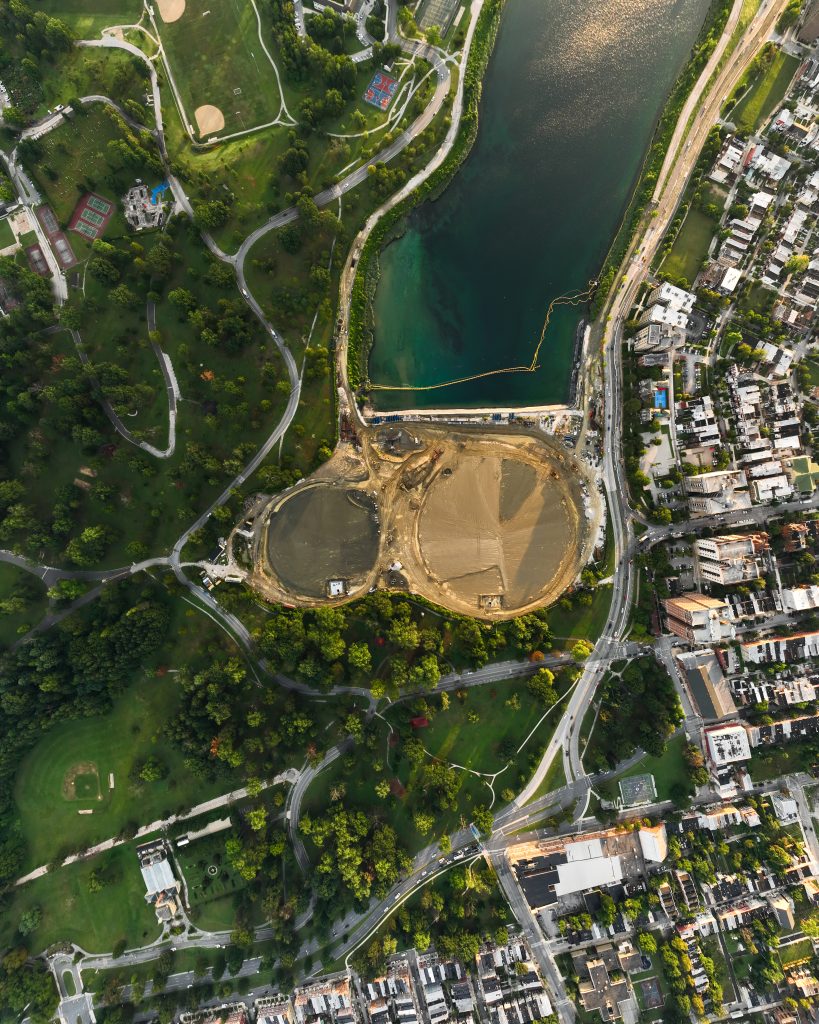
Water Storage Tanks Druid Lake Baltimore, MD
Baltimore, Maryland
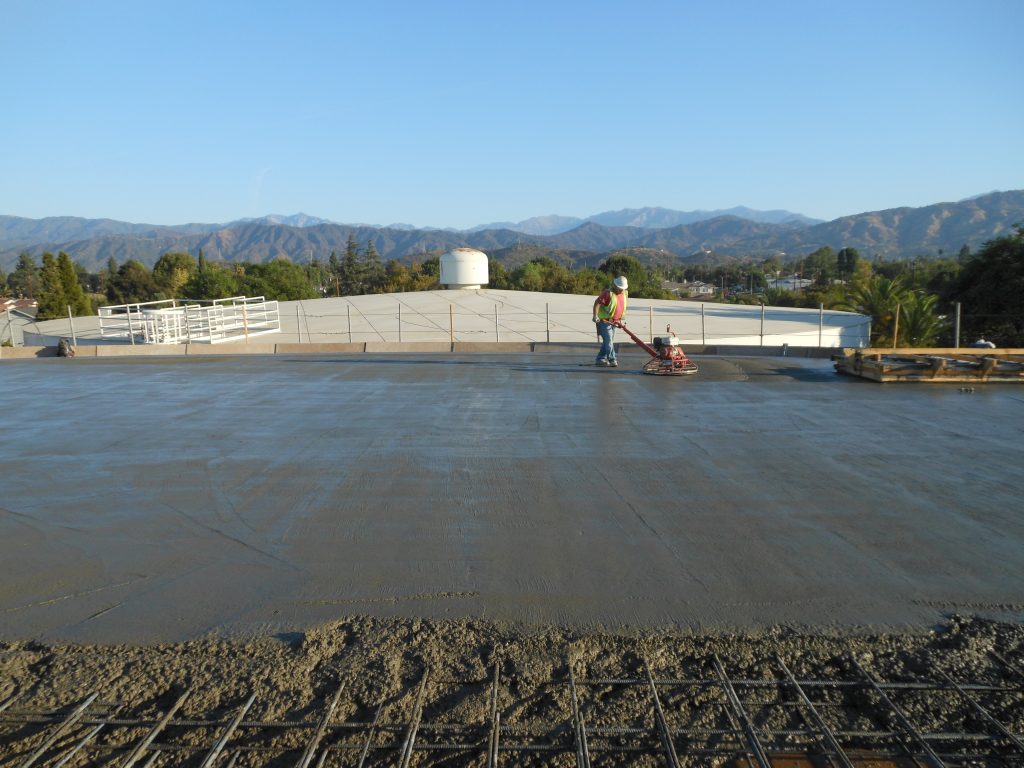
3.0 MG Charter Oak Reservoir Repair in Covina, CA
Covina, California
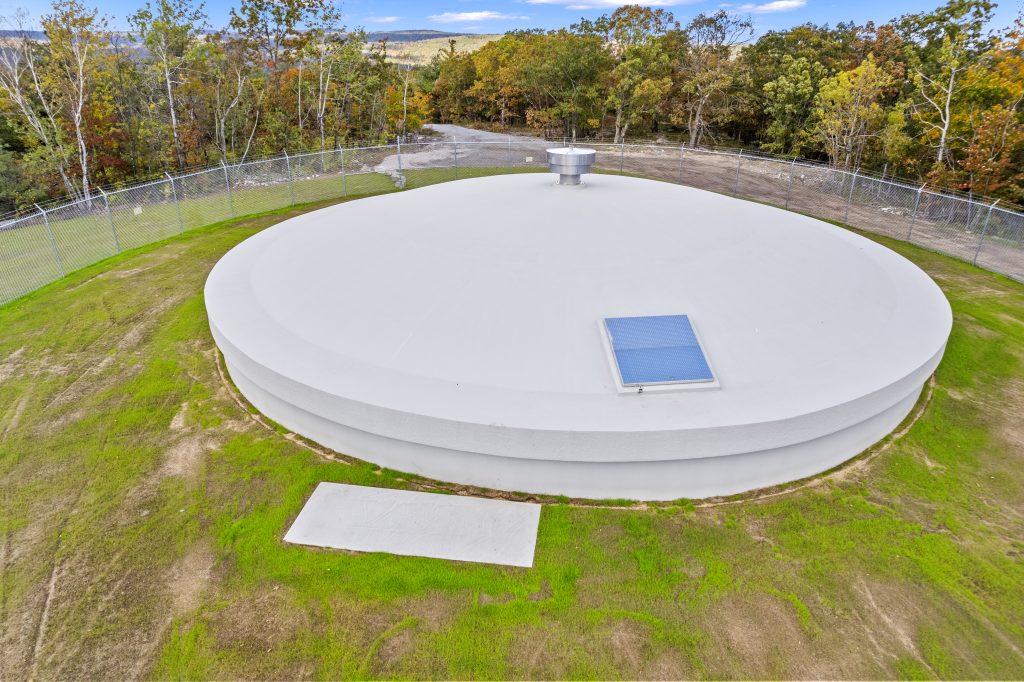
0.5 MG Oak Hill Water Storage Tank Replacement in Fitchburg, MA
Fitchburg, Massachusetts
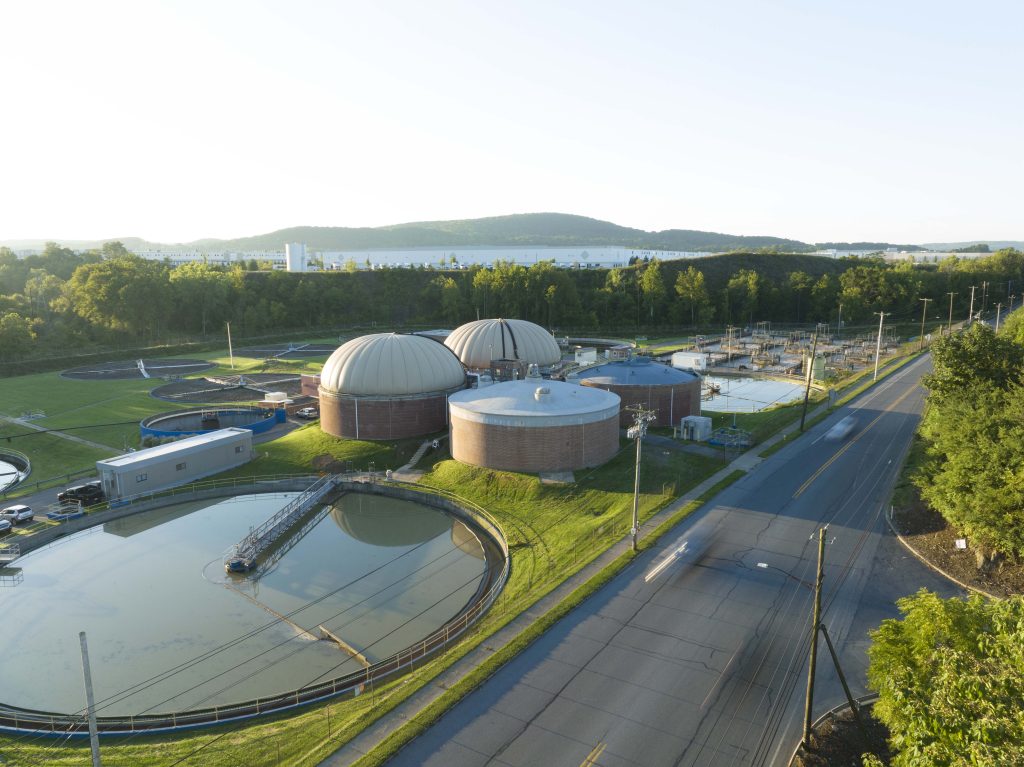
Dome Roof Rehabilitation in Bethlehem, PA
Bethlehem, Pennsylvania
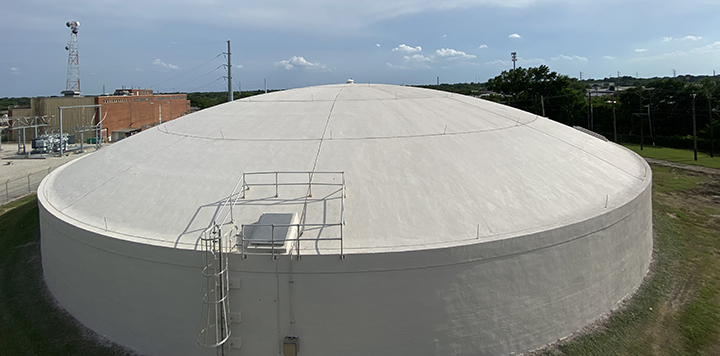
5.0 MG Water Storage Tank Rehab in Lavon, TX
Garland, Texas
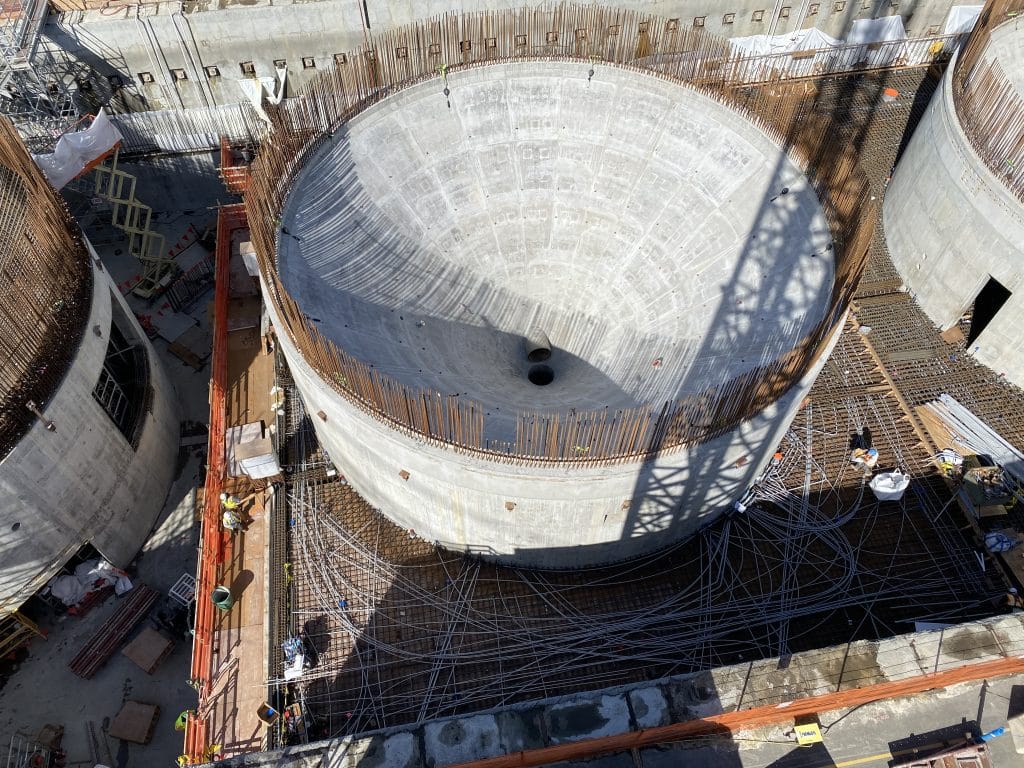

2 — 3.5 MG San Pablo Clearwell & Rate Control Station Replacement Kensington, CA
Kensington, California
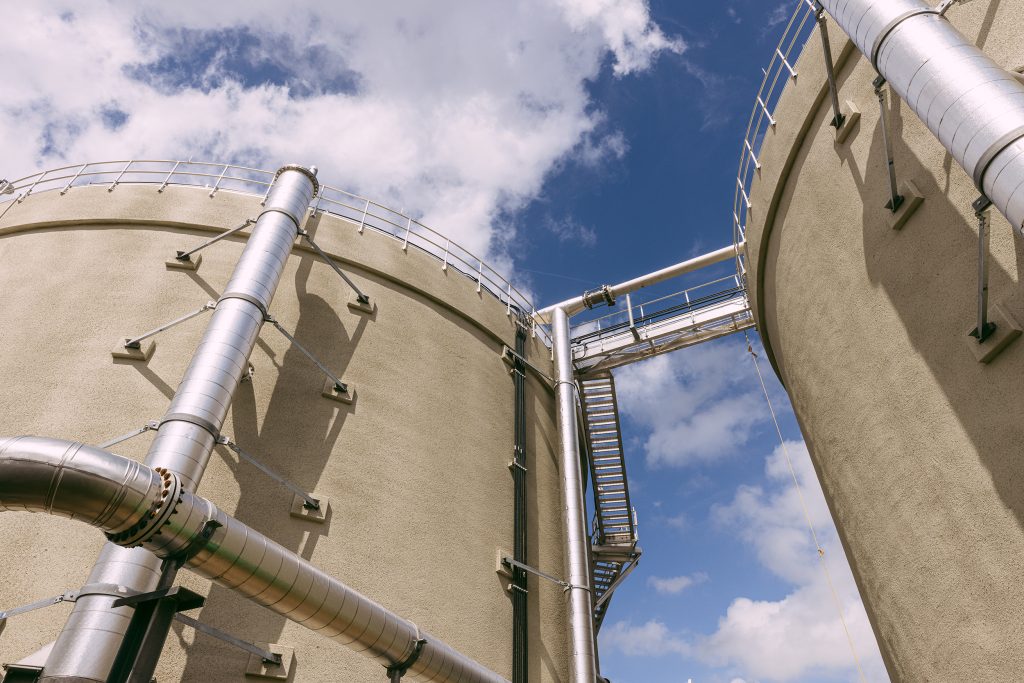
2 — 1.5 MG Digesters Piscataway Bioenergy Project WSSC Water, Accokeek, MD
Accokeek, Maryland
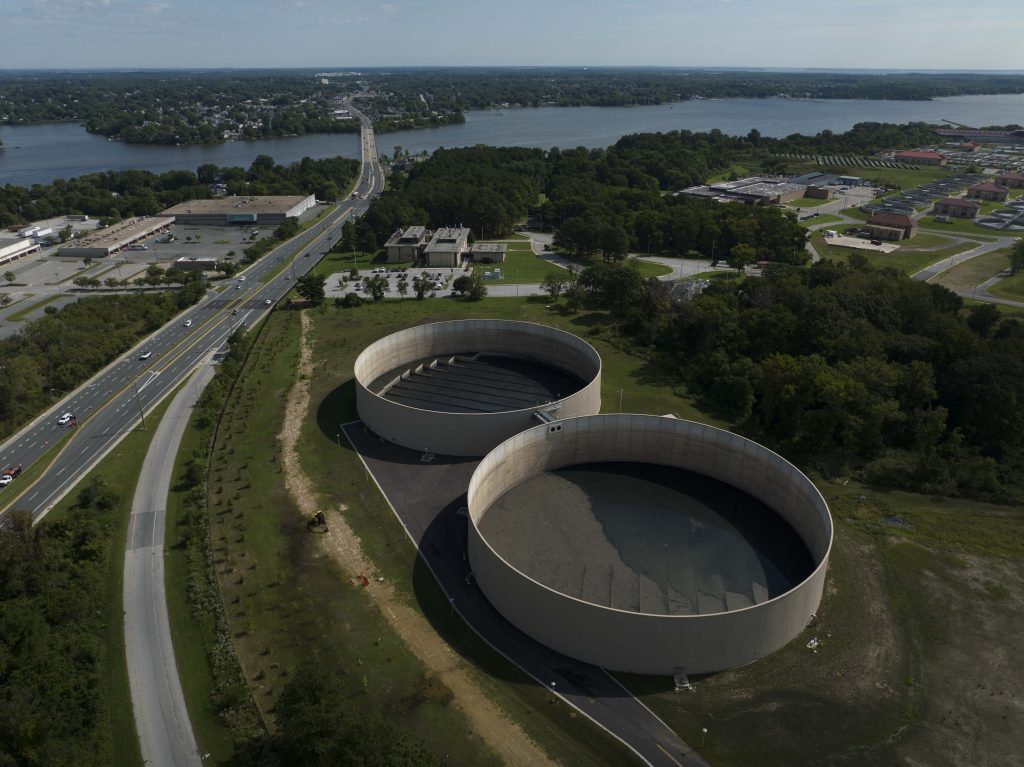
2 — 18.45 MG Tanks Back River Wastewater Treatment Plant Baltimore, MD
Baltimore, Maryland
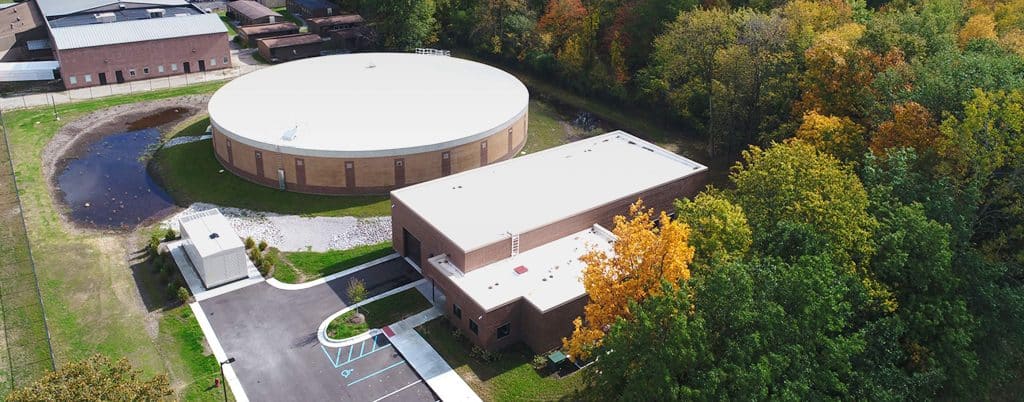
2.6 MG Canton Water Storage Implementation in Canton Township, MI
Canton Township, Michigan
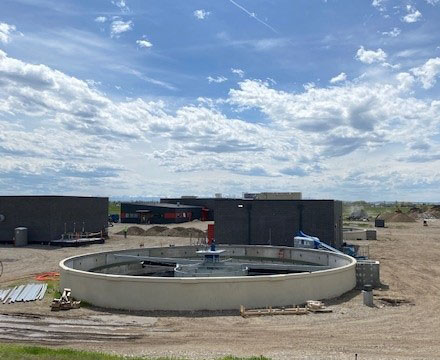
2 — 0.47 MG Belgrade Water Reclamation Facility in Belgrade, MT
Belgrade, Montana
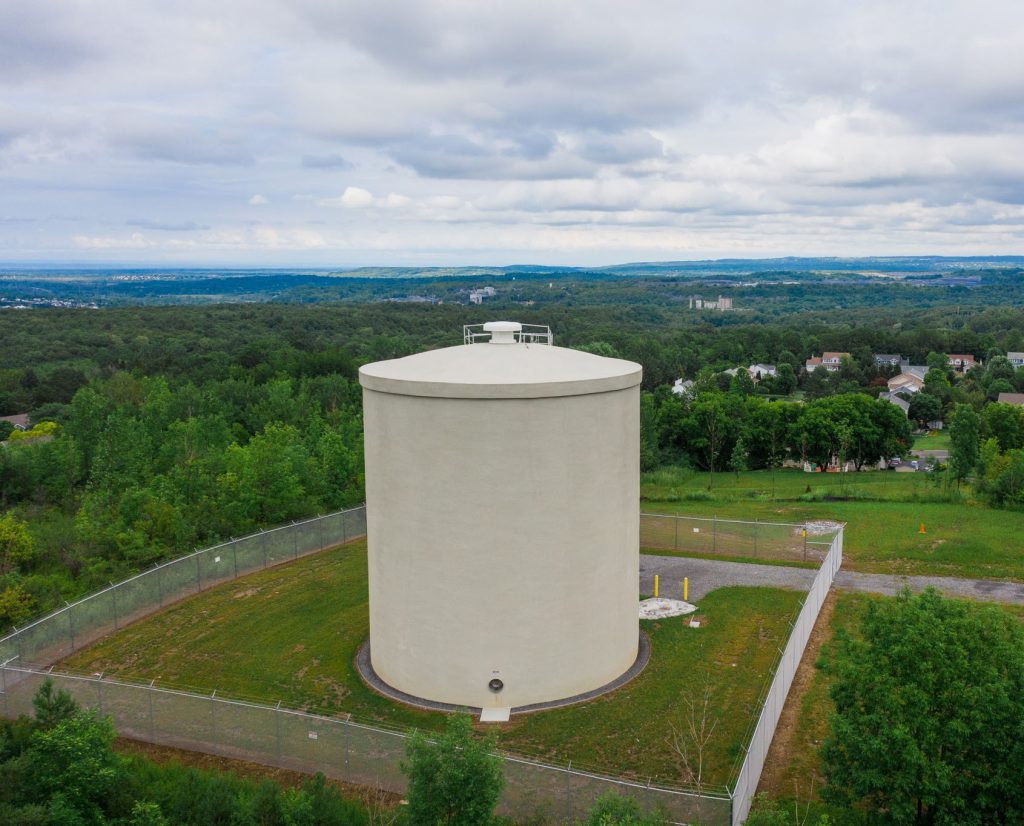
0.5 MG Southwood & Skyview Tank Replacement in Camillus, NY
Camillus, New York
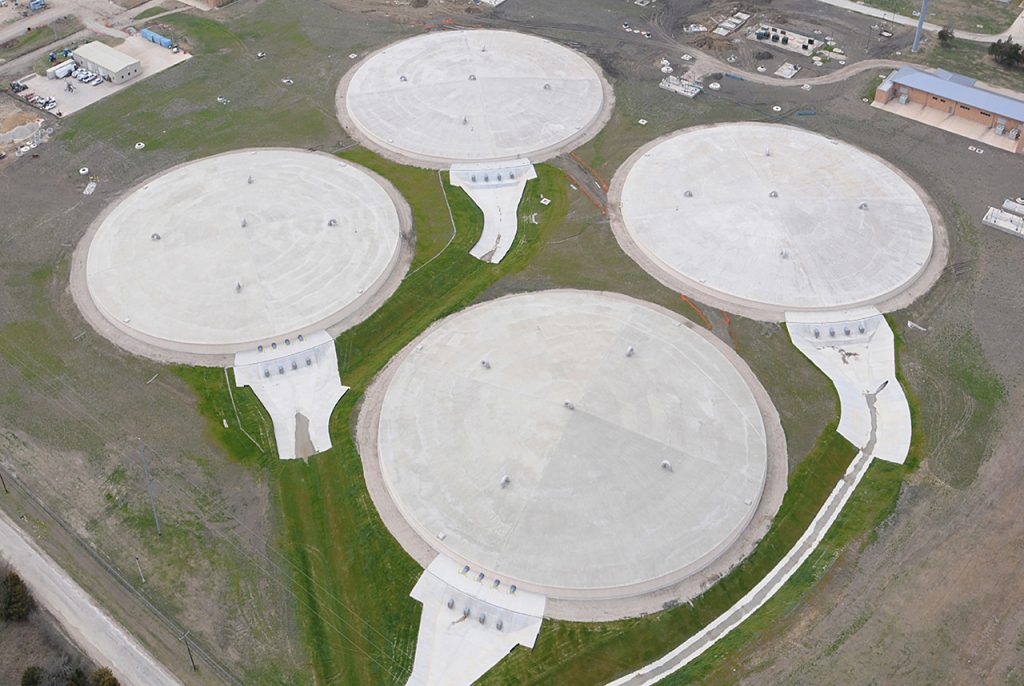
4 — 16.0 MG Eastside Water Treatment Plant, Dallas, TX
Dallas, Texas